system engineering, multi-physical modelling, control system design, artificial intelligence
Speed up your innovations – Secure your developments
It is with commitment, know-how and pragmatism
that we work with the largest industrial groups
AMONG OUR COMMITMENTS
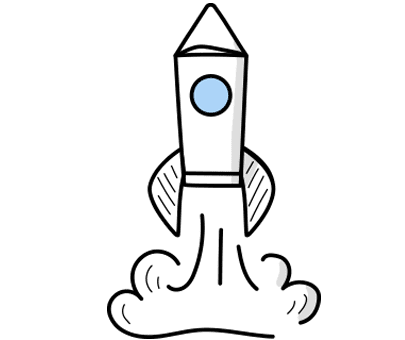
Boosting your innovation
thanks to our massive investment in R&D and our involvement in numerous research projects and competitiveness clusters
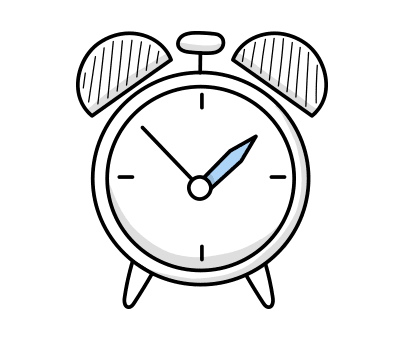
Saving you time
for the development of your projects thanks to the capitalisation of our experience and know-how and the wealth of our business libraries
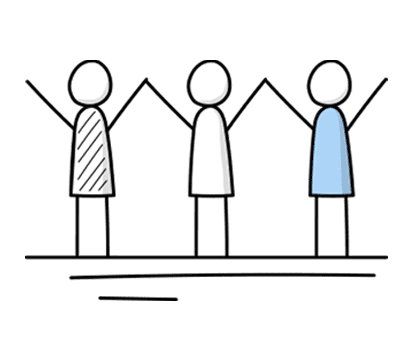
Cultivating well-being at work
to enable our employees to give the best of themselves, to progress and to develop by finding the right personal balance
NEWS
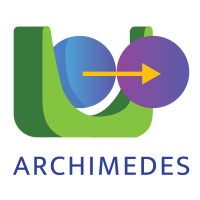
ARCHIMEDES Project
The pioneering EU research project ARCHIMEDES started on the 1st of May 2023. The KDT JU co-funded project aims to reach five main objectives: to pave the way towards a new area of technological advances that will realise trusted extended Lifetime and MTBF for GaN, SiC, MEMS devices monitored with...