ingénierie système, modélisation multiphysique, contrôle-commande, intelligence artificielle
Accélérez vos innovations – Sécurisez vos développements
C’est avec engagement, savoir-faire et pragmatisme que nous intervenons
auprès des plus grands groupes industriels.
PARMI NOS ENGAGEMENTS
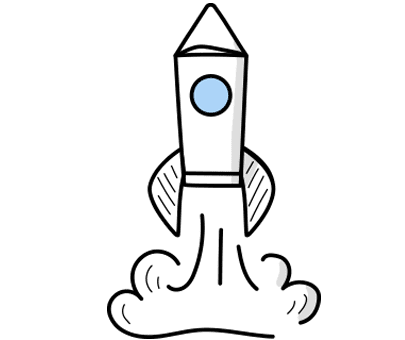
Booster votre innovation
grâce à notre investissement massif en R&D et notre implication dans de nombreux projets de recherche et pôles de compétitivité
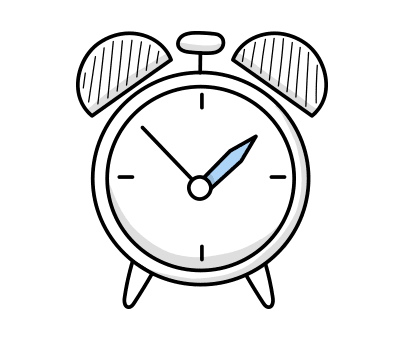
Vous faire gagner du temps
pour le développement de vos projets grâce à la capitalisation de nos expériences et savoir-faire et la richesse de nos bibliothèques métiers
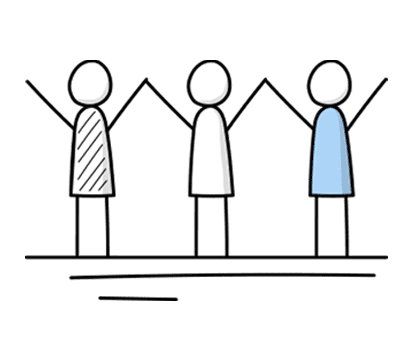
Cultiver le bien-être au travail
pour permettre à nos collaborateurs donner le meilleur d’eux-mêmes, de progresser et de s’épanouir en trouvant un juste équilibre personnel
ACTUALITÉ
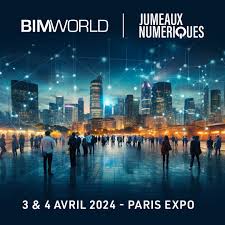
BIM World – Jumeaux Numériques
Le 3 et 4 avril dernier, SHERPA Engineering a participé au Building Innovating Managing (BIM) World. BIM World | Jumeaux Numériques est l’évènement incontournable en matière de construction numérique et d'aménagement durable. Le salon a accueilli plus de 10 000 participants, près de 350 exposants...